La pianificazione e la produzione digitale (non) sono un'arte
Hofmann – your driving force | Lichtenfels, Germany
In tool and machine manufacturing, smart MES- and CAM-supported production opens the door to maximum efficiency
Tool and machine manufacturer Hofmann – your driving force is active in many industries, and its production uses a wide range of technologies and software. The Hummingbird agile Manufacturing Execution System (MES) was developed precisely for such complex scenarios: It digitizes, visualizes, plans and controls all processes in real time and communicates with over 60 machines and a wide range of connected systems at Hofmann. Since 2022, it has also been working with hyperMILL® CAD/CAM software from OPEN MIND, which brings tangible benefits for GROB production lines.
Siegfried Hofmann founded the family business in Lichtenfels in 1958. In the same year, he set up his first lathe in a garden shed, which was the company's first building. Today, it has grown into an internationally active company with two large production and assembly plants, now in its third generation, supplying customers in 25 countries. The company name speaks for itself: Hofmann – your driving force. With a strong focus on research, the Lichtenfels-based company and its 300 employees develop and produce sophisticated tools for all injection molding processes, innovative technologies for mechanical engineering, such as for resource-saving particle foam processing with the company's own product BEAD.MACHINE, and novel solutions in 3D metal printing. Last but not least, contract manufacturing involves the series production of individual components, assemblies and machines.
„Hummingbird visualisierte erstmals unser gesamtes Fertigungsgeschehen und schuf sofort Transparenz. Die richtigen Informationen standen zur richtigen Zeit zur Verfügung. Dies senkte das Fehlerrisiko deutlich und optimierte Produktivität und Liefertreue.“
Markus Striegel, Process Engineer at Hofmann
This extraordinary portfolio not only serves a wide range of industries, such as automotive or medical and packaging. It also requires highly efficient and intelligent planning and control of manufacturing and automation. Hofmann therefore turned to comprehensive digitalization at an early stage, initially with data processing software for operating the various automation systems. This monolithic solution enabled seamless data communication, but limited system utilization due to its uniform cell management system. It also provided no assistance with production planning or control, and a solution was sought for this as well, because previously the valuable know-how for this was only in the heads of the production management.
The Hummingbird MES was designed to provide answers to precisely these questions, which are of concern to many companies in the tool and machine construction sector, as well as in the production of individual parts and small series. An initial version of the MES was implemented at Hofmann in 2017 as part of the purchase of a new milling line consisting of four Hermle C42 machining centers.
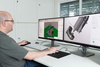
Hofmann has been using the CAD/CAM solution hyperMILL® for its roughing and drilling applications since 2022. Carsten Walther, CAM programmer, emphasises the flexibility in 5-axis simultaneous milling: ‘hyperMILL® automatically calculates all the angles of incidence, and it is very flexible to work with. The bottom line is that it provides greater accuracy, less risk of errors and saves an enormous amount of time.’
Hummingbird MES: high-level planning and control
The advantages were immediately apparent: ‘Hummingbird visualized our entire production process for the first time and created immediate transparency. This enabled us to plan deadlines and assign responsibilities and tasks to employees and resources. The complete detailed planning was now paperless and digitally mapped, processes could be planned in a resource-oriented manner and controlled in real time. The right information was available at the right time. This significantly reduced the risk of errors and optimized productivity and delivery reliability,’ says Markus Striegel, process engineer at Hofmann – Ihr Impulsgeber, who was responsible for process optimization when the MES was introduced, summarizing the initial successes. With the help of Hummingbird, Hofmann soon bundled the previously separate capacities of toolmaking and production engineering, including resources, in the MES. Since then, both areas have been able to use personnel and materials across the board and thus more efficiently.
The problem of system integration has also been solved. Hummingbird does not offer its own application software for many systems like a monolithic system. Instead, the MES integrates any machine and automation system as well as all common operating systems, including systems such as ERP, PPS, CAD/CAM or PDM/PLM. At Hofmann, Hummingbird is now connected to the overarching ERP system and controls over 60 machines, including manufacturing centres for milling, turning, eroding, wire cutting, grinding, drilling and measuring. Even in-house developments by companies can be connected via an open API interface – a philosophy that is fully in line with the networking concept of Industry 4.0.
Markus Striegel lists further advantages of the Hummingbird process: ‘Digitalization enables exactly repeatable processes, so that a part is manufactured in exactly the same way the second time as the first. This ensures traceability and ensures quality as well as the sequence of operations. The next step cannot be started until the previous step has been completed correctly. For example, machines can only be started after the CAM simulation has been completed. If process-related problems occur despite simulation, it is always possible to provide feedback to the CAM programmer.’
A great feature for GROB machines: hyperMILL®
Of course, CAM integration is an important topic. In 2022, Hofmann started using hyperMILL® CAD/CAM software from OPEN MIND for roughing and drilling applications. The ‘manager’ of the program deployment is the Hummingbird MES, which acts as an interface between CAM programming and the workshop, taking over NC data and drawings, visualizing them and making them available to the machines in the planned sequence. As a rule, operators only have to check them and start them at the push of a button.
hyperMILL® operates a complete, newly purchased production line with six milling centers from GROB. ‘These machines have completely different kinematics than the other machining centers we usually use. We did not have any success with our existing post-processor for converting CAM data into CNC code, for example, when we wanted to measure on the machine or probe parts. We also encountered problems when using new technologies, such as barrel milling cutters. That's when we came across hyperMILL®. We had seen this software solution in action at events held by a wide variety of machine tool manufacturers. The flexibility, powerful strategies and innovative technologies convinced us. We wanted to break new ground and take advantage of the complete CAD/CAM package,’ said Martin Wegner, Hofmann's Production Manager, describing the initial situation.
hyperMILL®'s “dress rehearsal” at Hofmann was a success story in itself. ’The hyperMILL® expert came and we managed to get a program running on the machine relatively quickly at the first attempt. Without an interface – we couldn't believe it,’ says Martin Wegner. What was and is interesting for Hofmann is that hyperMILL® introduced its own post-processor technology that can be used on machines and controllers from a wide range of manufacturers. This eliminates the need for individual solutions from third-party providers, which can lead to information loss. In the case of GROB, hyperMILL® was able to post the original machine code.
Not only that: Hofmann's machine operators can now use the hyperMILL® SHOP Viewer to view and simulate the finished CAM data right next to the machine. CAM programmer Carsten Walther is enthusiastic about the hyperMILL® VIRTUAL Machining Optimizer: ‘It automatically finds the best technical, collision-free approach and optimal process movements. It analyses the NC program during the NC code generation and adapts it perfectly to the machine kinematics. This reduces the programming effort and the optimized connection movements significantly reduce non-productive times.’
Martin Wegner particularly likes the hyperMILL® Probing module for in-process measurement and inspection on the machine: ‘hyperMILL® directly outputs reliable measurement programs, which are then distributed by Hummingbird MES. All these useful tools ensure greater reliability and quality, as well as shorter throughput times.’
Setting the pace: hyperMILL® MAXX Machining, 5-axis and macro technology
When it comes to 5-axis simultaneous milling, which is used for example in rest machining, Hofmann benefits from the many years of expertise in this sector that hyperMILL® provider OPEN MIND has to offer. ‘The CAM software automatically calculates all the angles, which allows for a high degree of flexibility when working with a limited selection of standard tools. The bottom line is greater precision, a lower risk of error and huge time savings,’ says CAM programmer Carsten Walther.
The roughing module from the hyperMILL® MAXX Machining performance package is also used: Hofmann's CAM programmers use it to generate trochoidal toolpaths. This makes it possible to machine a large amount of material quickly, efficiently and gently. ‘Programming is very quick and easy. We use the module for roughing with indexable inserts, for example, where it significantly improves tool life,’ says Carsten Walther, who also highlights the feature and macro technology of hyperMILL®: ’This allows us to save and recall repetitive machining sequences as macro modules. It works perfectly and saves programming time.’
The programmer also praises the simple hyperMILL® user interface, the fact that the software is easy to learn and the support provided by the digital program assistant at work, which reduces the risk of errors. ‘We are also very satisfied with the support and application engineers at OPEN MIND,’ says Carsten Walther.
Hummingbird integration
Thanks to Hummingbird integration, hyperMILL® and Hummingbird MES are perfectly harmonized. This is not just further proof of the high compatibility of both systems. OPEN MIND is a majority shareholder in the manufacturer Hummingbird Systems. And is striving for an even deeper integration of MES and CAM systems in the future. As a long-standing development partner, Hofmann should be pleased about this – and benefit from it at an early stage.